What is packaging?
The Japanese Industrial Standards (JIS) define packaging as “the appropriate materials, containers, and the operations to store goods in them, as well as the techniques and states of applied to them, for the purpose of maintaining the value and condition of those goods during their transportation, storage, trading, use, etc.”
The Role of Packaging
The basic roles of packaging are protection, convenience, and comfort.
Protection
- To prevent damage and deformation due to impact, and keep foreign substances out.
- To prevent oxidation and spoilage.
- To protect against pests and putrefactive bacteria
- To prevent tampering by human hands.
Convenience
- To provide to consumers necessary information such as ingredients, cooking methods, and expiration dates.
- To carry out product branding as a sales promotion tool.
Comfort
- To enable the transport of large quantities at a time.
- To be able to withstand impacts.
- To provide information.
- To be easy to store and keep.
Packaging configuration must be chosen according to the intended purpose and the conditions to fulfill.
Packaging involves a variety of tasks, which can be broadly classified into three categories.
Packaging operations
Filling
Filling a pre-made container (or one in the process of being made) with a fixed quantity of contents
Wrapping
Covering one or more pieces of the contents with a flexible material
Boxing
Packing the contents into a pre-made box (or one in the process of being made).
Packaging Machines Produced by Omori Machinery
Introducing the 4 types of packaging machinery that are Omori’s mainstay products:
We have form-fill-seal machines that can flexibly handle all kinds of products, thermoformers that can seal products in a vacuum state,
tray wrappers for packaging food products in trays, and cartoners and casers used for box assembly and packing.
Horizontal Form-Fill-Seal Machine
Horizontal form-fill-seal machine feeds products horizontally on a feed conveyor, wraps them while forming film into a cylindrical shape, seals products at both ends, and cuts the film.
This machine is widely used for a broad range of products, from food products to industrial products, because of its simple structure, dual-use properties, versatility, and adaptability to a wide variety of film types.
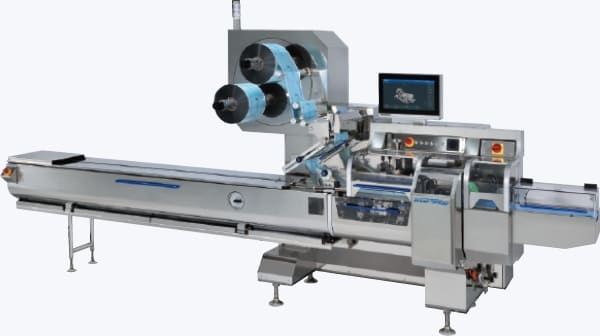
Thermoformer
Thermoformers are often used to keep food fresh and flavorful by removing air (oxygen) from inside the package after it is hermetically sealed with extremely low air permeability film.
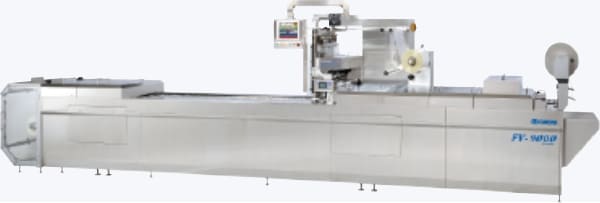
Tray Wrapper
Tray wrappers place products on trays and wrap them with stretch film.
They are widely used in supermarkets for packaging meat and prepared foods.
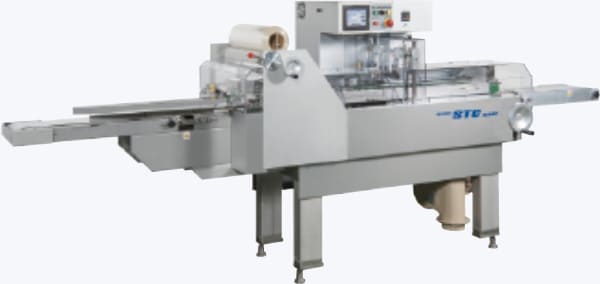
Cartoners & Casers
Cartoners make the interior of the product package, while casers make the exterior, such as corrugated board for shipping.
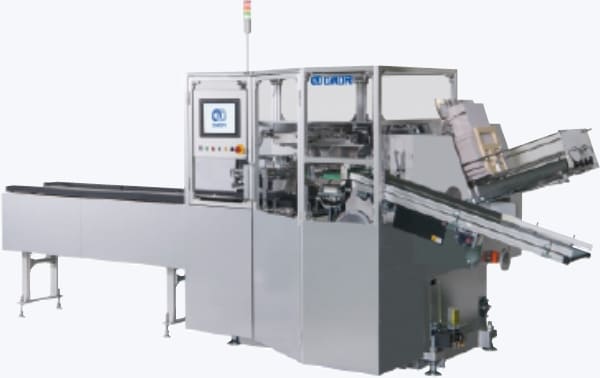
Horizontal Form-Fill-Seal Machines
These machines are used for packaging a variety of products, from food and daily goods to clothing.
There are 2 types of horizontal form-fill-seal machines: top film feed machine and inverted machine.
Horizontal Form-Fill-Seal Machines
- Top film feed
- Inverted
With top film feed wrapping, the film roll is installed above the height of the product being conveyed,
while in Inverted wrapping, the film roll is installed below.
Top film feed wraps the product from above and is suitable for wrapping individual products.
In contrast, Inverted wraps products sitting directly on the film and is used for wrapping multiple products and packaging under special conditions.
Although top film feed is commonly used in automatic horizontal form-fill-seal machines, we will explain the process with Inverted, which is easier to understand.
Packaging process overview
- Feeding
- Forming
- Center seal
- End seal
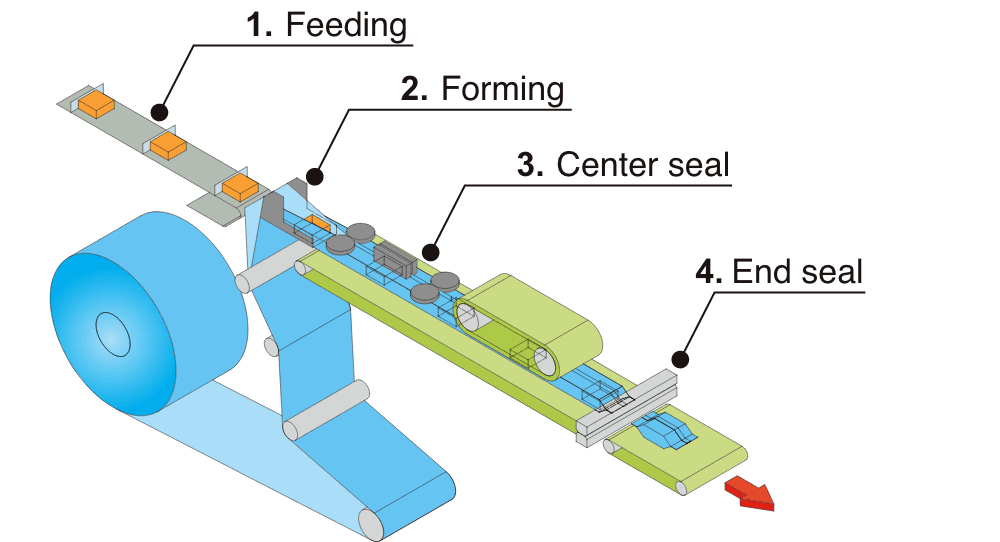
Horizontal form-fill-seal machine process flow can be roughly divided into 4 steps: feeding, forming, center sealing, end sealing.
STEP1Feeding
First, a finger fin or belt conveyor is used to supply products. The method is selected according to the characteristics of the product to be packaged, and the product is aligned and conveyed.
STEP2Forming
The film flowing from below is formed into a cylindrical shape and the product is wrapped. Since the products cannot be touched in subsequent processes, they have to be lined up in regular intervals here.
STEP3Center seal
Both ends of the film are sandwiched from the outside and heat is applied to make the center seal.
At this time, overhead product control belt are held down to prevent contents from shifting inside. Depending on the product, a brush or vacuum may be used to lightly press down the film as it is conveyed.
STEP4End seal
The cutter-equipped top and bottom plates simultaneously adhere to and cut the product. Horizontal form-fill-seal machines are often suitable for packaging large quantities of the same product.
This packaging machine can be used for a wide variety of products, with the exception of liquids and products that come apart easily.
By applying and altering horizontal form-fill-seal machine to change the way a bag is made or sealed, it can also perform 3-side seal wrapping, 4-side seal wrapping, and shrink wrapping.
- 3-side seal wrapping
- 4-side seal wrapping
- Shrink wrapping
Thermoformers
These machines are often used for packaging sliced ham and sausages.
The bottom film is softened by heat and made into a mold. The product is then placed in the mold and top film is sealed from the top.
Packaging process overview
- Forming
- Feeding
- Sealing
- Cutting
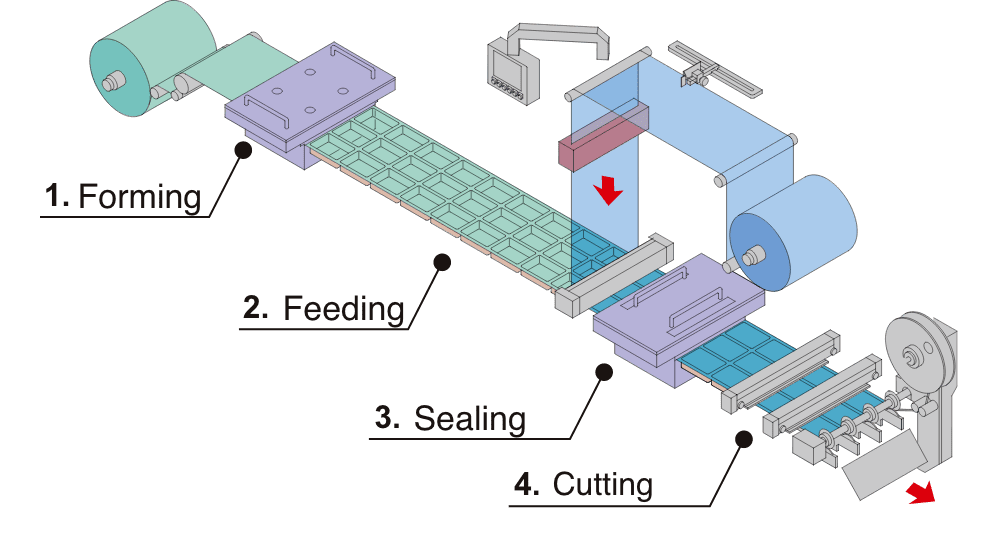
The thermoforming process can be roughly divided into four steps: Forming, feeding, sealing, and cutting.
STEP1Forming
A mold is placed over heated and softened bottom film to form a depression in the film with the force of compressed air. Depression shape is determined by the mold in the Forming section, so various depression shapes can be made by changing the mold.
STEP2Feeding
Contents are automatically or manually put into the Formed film.
STEP3Sealing
The film is joined with the top film that was set on top. When the overlapping films are sealed, the air inside is removed, creating a vacuum.
STEP4Cutting
The sealed products are set vertically and horizontally, and cut in turn.
Vacuum packs are often used to enhance shelf life through the packaging, but depending on the nature and use of a product, gas, steam, or skin packs can also be used.
Non-vacuum packing is also possible.
Examples of non-vacuum blister packs include packaging for pharmaceuticals and industrial products.
Tray Wrappers
A tray wrapper is a machine that film-wraps products placed on trays.
Packaging process overview
- Feeding & Forming
- Cutting
- Folding
- Discharging
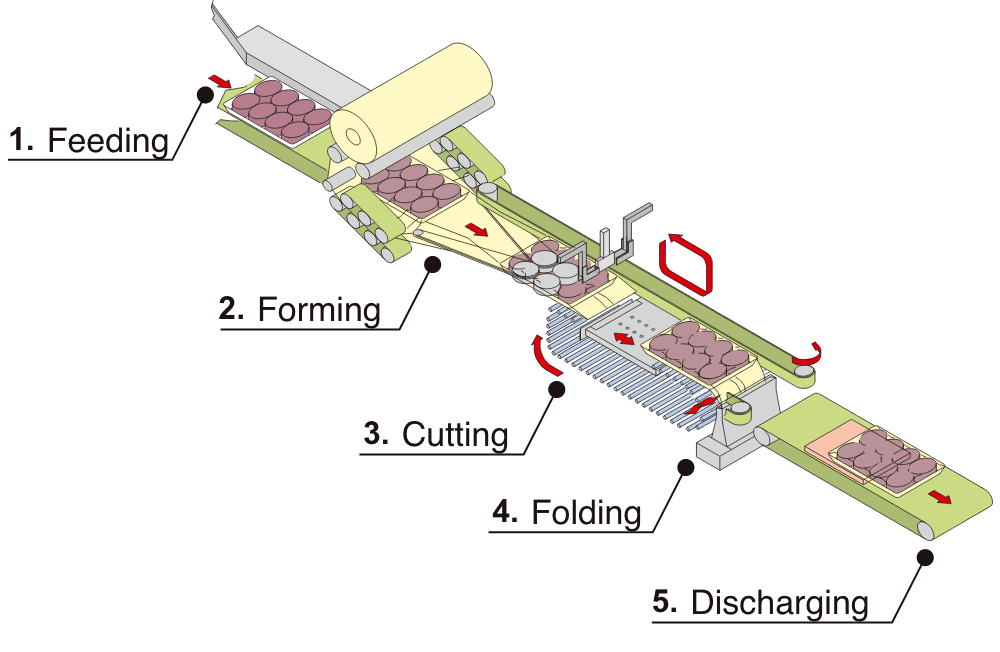
Tray wrapping operations can be roughly divided into four steps: feeding & forming, cutting, folding, and discharging.
STEP1Feeding & Forming
Film set on top is formed into a tube shape, and the product on the tray is fed into the tube.
STEP2Cutting
The film is cut at the product front and back.
STEP3Folding
The cut film in front of and behind the tray are taken to the underside of the tray via the movement of the roller conveyor and the transition of air.
STEP4Discharging
As the tray passes through the discharge conveyor, it is heated from below by a heater to make the film adhere to it. Since stretch film is used for packaging, it can be adjusted to various shapes.
Any product on a tray can be accommodated.
Cartoners and Casers
Cartoners are used for the interior of product packages, while casers are used for the exterior of corrugated cardboard boxes for shipping and other packaging.
Cartoners and casers can be divided into 2 types depending on the shape of the boxes to be used.
Packaging process overview
- Folding
- Feeding
- Gluing
- Sealing
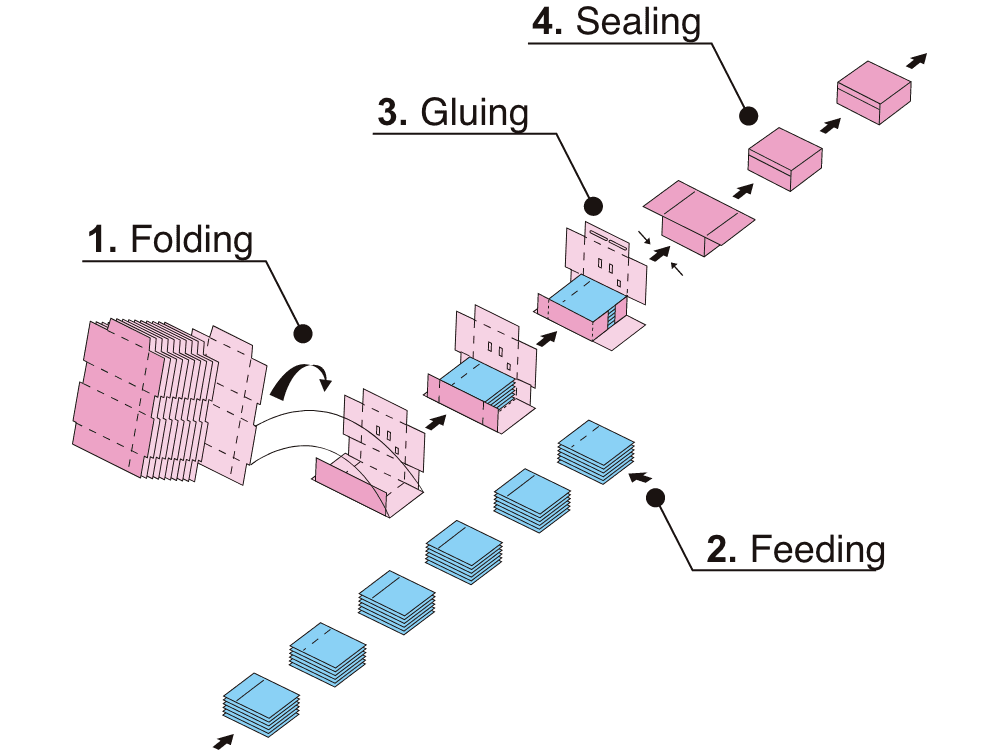
The machine’s mechanism can be roughly divided into 4 steps: folding, feeding, gluing, and sealing.
STEP1Folding
Blank sheets are folded, assembled, and transported along the guides.
The flaps, which are edges of the box with broken lines, are folded into a box shape.
STEP2Feeding
Products are fed into the box as it is being formed. Feeding methods, such as pushing in from the side, pushing up from the bottom, or lowering from the top, vary from machine to machine.
STEP3Gluing
Hot melt glue, a glue made by heating and melting plastic, is applied to the joining surfaces of the blank sheet.
STEP4Sealing
The folded parts are held down and sealed.
Cartoning and case packing are convenient for transport and display because packages are identical in shape and strong.
They may also be used for logistical protection or as storage containers.
Cartoners and Casers
- End load
- Top load
- Wraparound
A sheet before it is assembled into a box is called a blank sheet.
The wraparound method folds blank sheets into boxes.
In contrast, the end load method forms boxes by erecting cylindrical blank sheets.