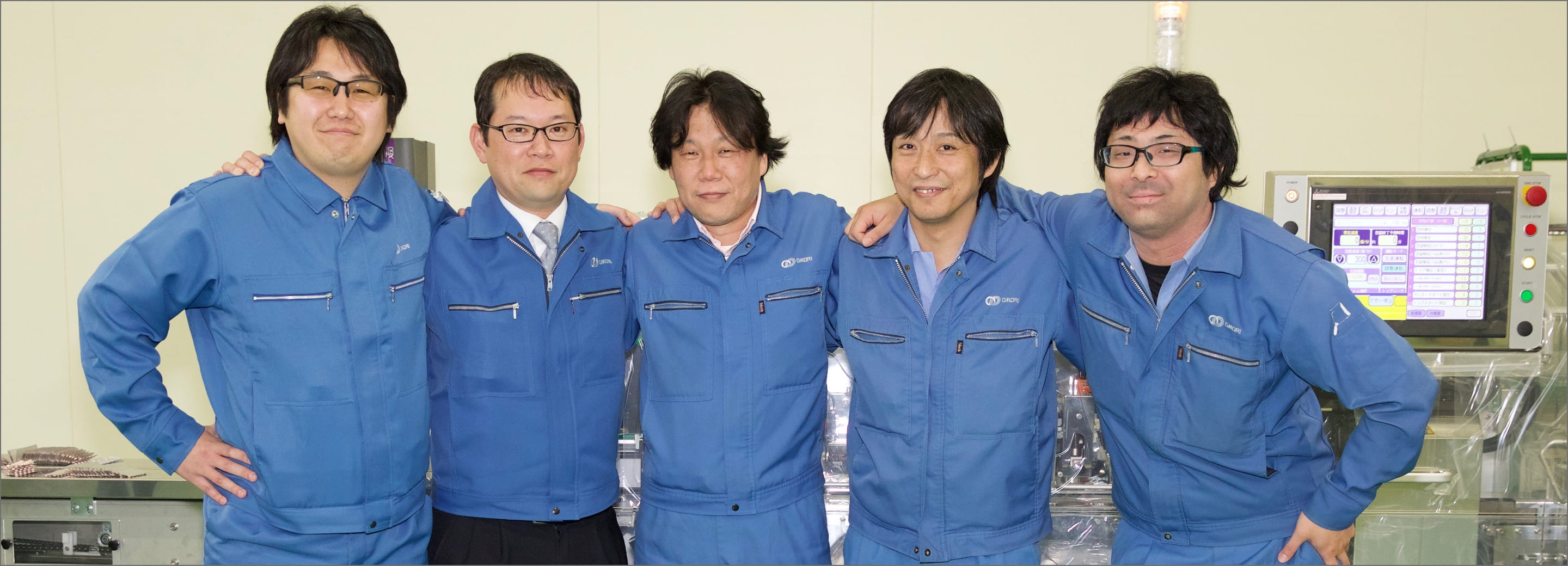
S-7680 High-Speed Horizontal Form-Fill-Seal Machine for Pharmaceutical Products
A project to review the fundamental design of conventional models, and develop a new machine
Since the 1970s, we have been developing packaging machines specialized for pharmaceutical products. Among these is the S-5680 which was completed in 2001 and became Omori’s leading packaging machine, gaining great trust from customers. However, ten years after initial development, some members of the company started to call for us to review the basic design. Therefore, in December 2014, a new project team was created and they started to develop the S-7680.
Although most high-speed pillow packaging machines tend to focus on processing speed, for this machine, we gave priority to improving the quality of the machine performance. Our most important task was to ensure that the level of reliability and durability was even higher than the S-5680. Since 3D CAD software became available in the year previous to staring, development was carried out while efficiently utilizing these software tools for strength calculation and motion simulation.
As for mechanical design, in order to realize high-speed operation, we improved the machine frame and drive unit. In addition to countermeasures against vibration, we also improved the rigidity of the cover ring. In terms of design, since the S-5680 had multiple minor changes, there were a lot of retrofit parts. There was also a desire to make these as well-designed as possible.
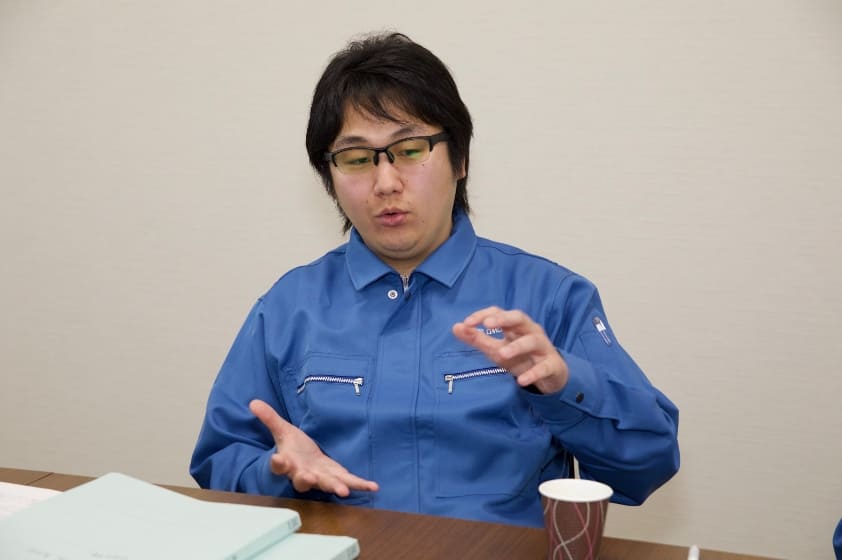
Each member of the project refined their knowledge and overcame all problems one by one
Each person in charge worked hard to advance the project while overcoming a variety of problems. However, there were many issues that could not be dealt with by ordinary means, and members were asked to work together and share their wisdom in order to resolve them.
From the start, it was important to ensure that the mechanical design created for the S-5680 was reliably incorporated into the S-7680. Until then, various optional functions were developed according to specific requests from our customers. However, this time we fine-tuned these options and included them as standard.
One of these standardized functions is the automatic size change function. This function allowed the conventional size adjustment procedure that required manual switching to be carried out automatically. This reduced work burden and eliminated the possibility of switching mistakes.
In regard to electrical design, the consideration of what kind of cooperation could be utilized to improve usability became a big issue. Under these circumstances, we worked on making changes such as improving the end seal pressure management and end jam detection.
In the S-5680, these devices were fitted to the front of the operation panel, and anyone could change the settings. This was a point for improvement from a security standpoint. Using the operation screen to change machine settings ensured security and gave it a cleaner appearance.
In terms of manufacturing, while confirming that there were no processing or wiring problems, and parts did not interfere with each other during actual assembly, we carefully considered feedback and worked with extreme care.
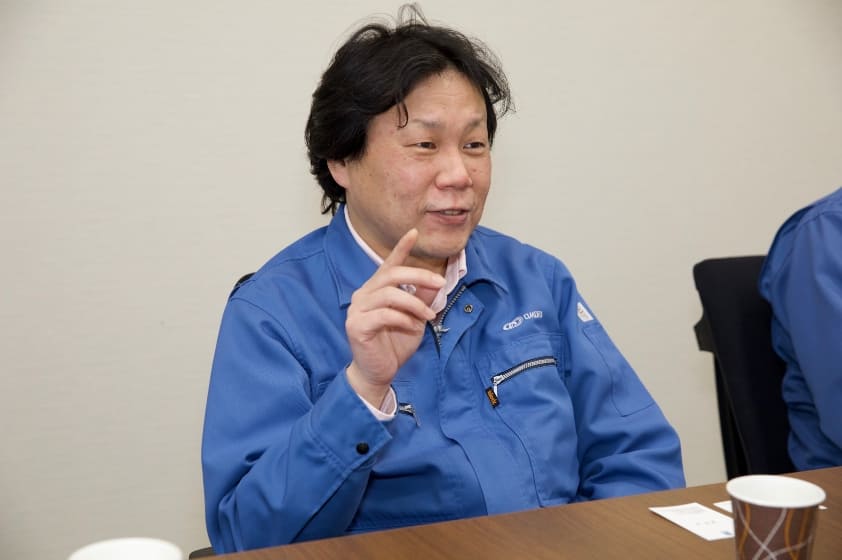
We never stop working to further improve our packaging machines. We believe that it is important to continuously follow up on customer requests.
After repeated trial and error, the S-7680 made its long-awaited debut at the Interphex Japan trade show in July 2015. At this trade show, our main aim was to expose more potential customers to the new model S-7680, and to receive feedback and first impressions from those in the industry. After confirming the responses to a survey we implemented at the trade show, we decided to change the design to lower the position of the operation panel. After that, the completed S-7680 was finally exhibited at the Japan International Packaging Machinery Show held in October of the same year.
However, even after its debut, the members of the project did not believe that work on this model was complete. Rather, some members even thought that this was merely the start of a new stage of development. This was mainly because of the need to remain flexible to cope with the changing production environment of pharmaceutical products. Our customers’ demands are getting more and more sophisticated, requiring packaging materials to become more diverse, production speed to be increased, and packaging quality to be improved.
We want to listen carefully to the voices of our customers, and carefully nurture the S-7680 so that it can continue to meet their demands.
PROJECT MEMBER
S-7680
- Pharmaceutical Sales Department, Sales Group
- As a person in charge of sales, I felt that it was my mission to make the S-7680 a successful product.There were times when I thought that progress was not going as well as expected, but I was extremely happy when it was finally completed.
I can never forget the even greater joy when we successfully delivered the first unit to a customer.
- Second Division, Engineering & Manufacturing Group Section 2, Mechanical Design Department 2
- As the new model was designed using new 3D CAD software, we were able to work with high efficiently even when we determined design policies such as device layout and verification of operability after consultations with various other related departments.
In the end, we were able to develop a new model that expanded on the technology created for the S-5680, and satisfied various customer requests.
- Second Division, Engineering & Manufacturing Group Electrical Design Department 2
- This new model was generally based on the previous S-5680, and I believe that this design choice contributed a little to improving ease of use.
As a member of the project team, during the development period I made sure to have open communication with each person from the electrical design department, and worked in close cooperation with the mechanical design and production departments.
- First Division, Engineering & Manufacturing Group Section 3, Production Department 1
- Even though we felt a natural sense of accomplishment upon completion of this machine, it was even more important to continue to respond to the needs of individual customers.
I believe that we should follow the major principle of working to reduce costs while keeping close communication with persons in charge of sales. The S-7680 still has a bright future ahead.
- Second Division, Engineering & Manufacturing Group Section 1, Production Department 2
- For this project, I was in charge of machine assembly. After trial assembly, confirming operation, and finally witnessing the first successful pillow packaging of a product sample, I really felt a great sense of relief from the bottom of my heat.
I worked in the trade show booth to explain the functionality of the machine to attendees. There I was able to listen to customers’ opinions and gauge their reactions. This feedback was then used to further improve the design of the machine.