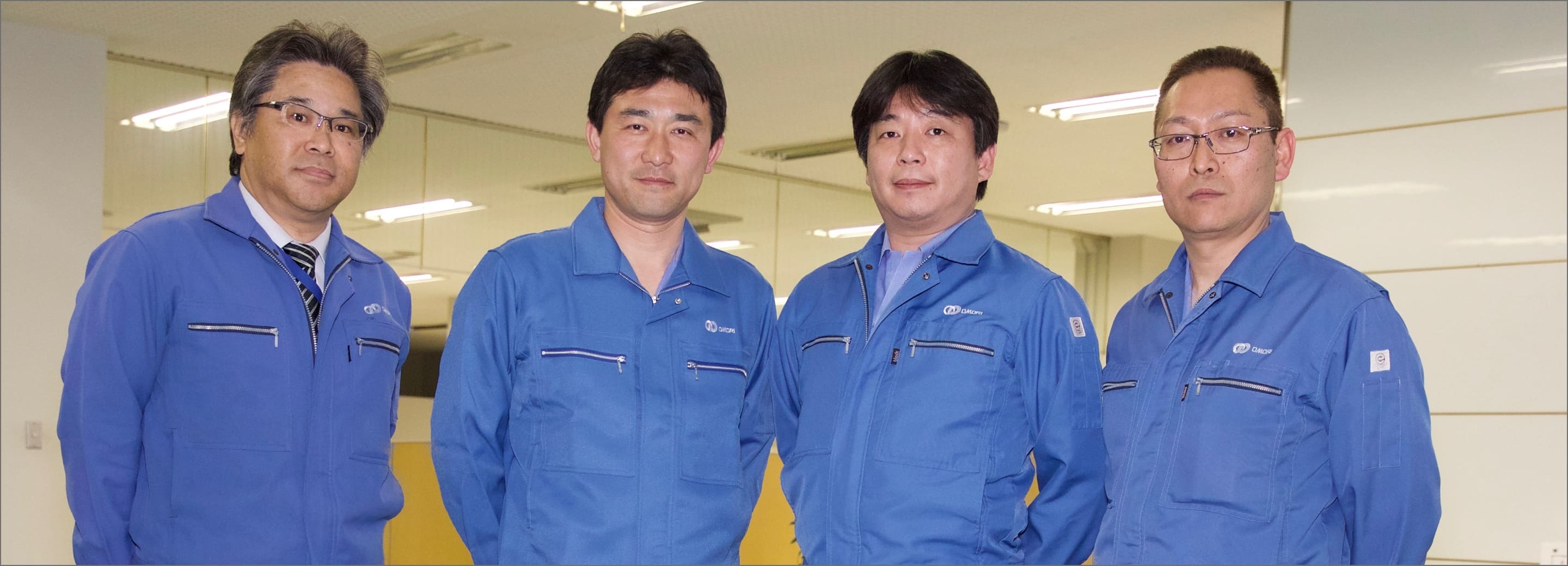
The Newly Evolved “EP-7000 High-Speed Horizontal Form-Fill-Seal Machine”
The goal to make a packaging machine that would still be popular even ten years into the future
In April 2004, members were recruited for a new project under the guidance of CEO and President Toshio Omori who was serving as vice president at the time. Around ten employees were selected from the mechanical design, electrical design, production, and procurement departments, and the service sections. The vice president told them that their task was to develop a new packaging machine that had never been seen before. He then asked each individual member to consider what type of product would suit the next generation. From then on, the members met each month and continued to hold planning and development meetings.
However, development of a new machine had to start with the search for an appropriate overall concept. At that time the concept of ecology began to become prominent, and there were more calls to incorporate power and energy saving functions. In fact, the E in EP-7000 stands for “Ecology.” However, truly creative ideas are not easy to come up with.
At that time, we were extremely lucky to hear the news that a large packaging machinery exhibition would be held in the US. Five members of the project were selected to investigate what types of functions were included in packaging machines in the US and Europe. The goal of the project team was to introduce Japanese machines to be used in the US and Europe, and to make a machine that would still be popular even ten years into the future.
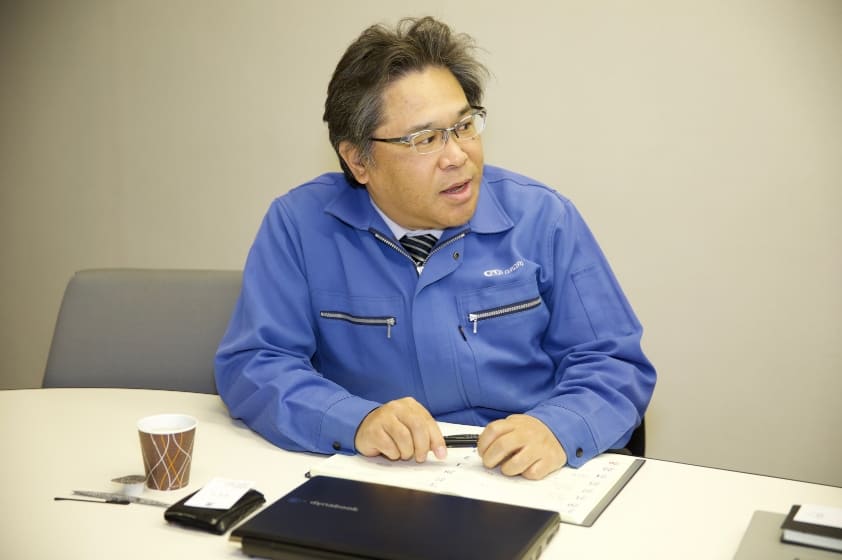
Overcoming unforeseen circumstances and adding new functions
The members of the project who visited the US felt that foreign packaging machinery had excellent design. US and European machines placed high priority on design, and in addition to the form of the entire line, the presentation of parts such as switches and panels was different to those made in Japan. To be used in the global market, machines needed the ability to be operated intuitively using visual indicators rather than words. All the members that visited the US had a good understanding of this upon their return. This experience eventually paid off in the form of our reception of the Good Design Award in 2008.
Now, new machines were to be developed by trial and error. As design, testing and verification were repeatedly being performed, an unexpected incident occurred during the prototyping stage. This was caused by structural modifications made to facilitate installation and removal of the end sealer cutter. These modifications increased the weight of the parts, leading to greater inertia, and the machine unexpectedly started to move on its own. However, changing the material to lightweight carbon fibers would place extra burden on the motor and reduce the rotational force. Eventually, we found a way to solve this problem by optimizing the pattern of motion. In this way, we overcame multiple problems and the new machine steadily approached completion.
Although previous models were equipped with a single touch panel screen, the EP-7000 was the first model to be able to be operated via dual touch panel screens. Although the single touch panel screen only allowed single operation, dual touch panel screens enabled two operations to be carried out simultaneously. By incorporating functionality that had never been seen before, we were able to greatly improve usability.
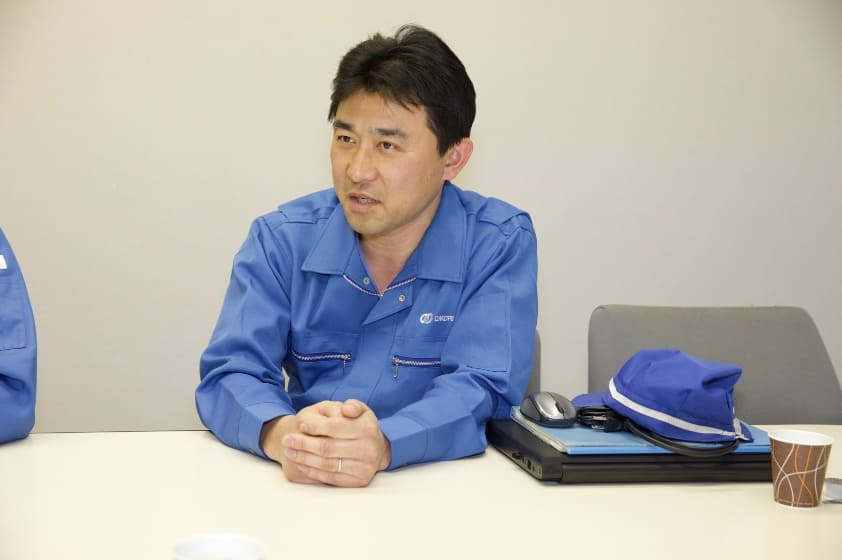
Converting the technology created during the development of the EP-7000 into core Omori technology
The EP-7000 that was completed thanks to the enormous amount of teamwork of the project members, had its debut at the Japan International Packaging Machinery Show held in October 2007. As a packaging machine that embodied the next generation of pillow packaging technology, it goes without saying that the unprecedented features and benefits highly impressed the attendees.
The unprecedented graphical display capabilities of the large 15-inch LCD touch panel that uses 3D images also became a hot topic in the industry. This machine was specially designed to make maintenance such as belt replacement easy. In addition to this, multiaxial servo motors were adopted to add various characteristic functions such as an increased ability to handle different packaging materials.
During the initial stages of development, project members visited the US to attend exhibitions and personally witness other global models. This experience was then utilized to increase members’ awareness of the need to focus on design. This naturally led to them being selected for the 2008 Good Design Award.
One project member remarked “The technology and functionality developed for the EP-7000 will be able to be utilized in subsequent machines. I am delighted that the technology that we worked so hard to develop will go on to become core technology of other Omori machines.” These words accurately expressed the uniqueness of the EP-7000 packaging machine that was developed completely from scratch without the support of any preceding technology.
PROJECT MEMBER
EP-7000
- Section 2, Sales Group
- We were able to successfully deliver the first unit to a well-established food manufacturer in 2010, two years after being exhibited at the Japan International Packaging Machinery Show. Although initially there was fierce competition, after actually using the EP-7000, it soon gained an excellent reputation. As a person in charge of sales, I am continuously working hard to further expand sales.
- R&D Division, Engineering & Manufacturing Group
- In addition to its ample functionality, we are also extremely proud of the fact that the EP-7000 is a packaging machine that has an optimum overall design that includes ease of maintenance. Upon starting development faced with many uncertainties, I investigated the design of all Omori machines to gain inspiration. This hard work finally resulted in a completed machine.
- First Division, Engineering & Manufacturing Group Electrical Design Department 1
- Since this design was started from scratch, there were many tasks that I had never encountered before. As Omori has their own specific control methods, the electrical design was also quite challenging. I believed that starting over again was the only way for an electric manufacturer to change their image, and I repeated this several times before the work was complete.
- Nagaoka Factory, Engineering & Manufacturing Group Manufacturing Department
- I was in charge of setting up the EP-7000 at the exhibition hall of the Good Design Award. As the products entered into the competition were competing for quality of design, I was determined to make the machine perfectly level to ensure that even the gaps between machine covers were uniform. I think that my involvement in the manufacture of this machine was a really valuable learning experience.